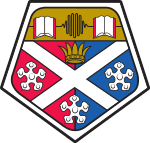
University of Strathclyde
Concerning the Venture
The College of Strathclyde is happy to have the ability to provide a extremely cross-disciplinary engineering mission on the method optimisation of high-value manufacturing. The place is hosted by the Division of Design, Manufacturing & Engineering Administration (DMEM) and is obtainable as a part of the Strathclyde Centre for Doctoral Coaching (SCDT) in AI-enabled Digital Excessive-Worth Manufacturing. The SCDT studentships are partly supported by the Nationwide Manufacturing Institute Scotland (NMIS) and Superior Forming Analysis Centre (AFRC), and college students will profit from alignment with a number of ongoing EPSRC analysis grants. Analysis undertaken as a part of this SCDT capitalises on new infrastructure funding made by the UK authorities into world-class forging capabilities on the AFRC, and collaboration with the Middle for Ultrasonic Engineering (CUE), the LiFi Analysis and Improvement Centre (LRDC), and with strategic associate Fraunhofer UK.
This PhD will give attention to the “in-process monitoring of microstructure evolution throughout ingot-to-billet conversion of the aerospace grade Ti-6Al-4V (Ti64) materials in assist of the continued improvement of Digital Twin infrastructure for high-value manufacturing”.
Forging stays the state-of-the-art manufacturing route for high-value elements that demand dependable structural integrity. Beginning with vacuum arc re-melted ingots at elevated temperatures, tightly managed thermomechanical processing is carried out. A number of open-die forging hits and reheats could also be required to refine the inhomogeneous as-cast microstructure. Latest enhancements in management, sensor and materials testing expertise have been launched as a part of trade 4.0 and digital-twin necessities, however to take full benefit these should be coupled with strong and verified fashions of the bodily deformation mechanisms and paths and in-process optimisation algorithms/methodologies for direct operation of kit, management of course of and finally determination making with minimal to no uncertainties. That is solely achievable by means of new and data-centric approaches that brings collectively data and know-how of supplies behaviour, simulation and modelling, sensing, knowledge evaluation and optimisation, and most significantly synthetic intelligence with determination making functionality.
An infrastructure for DT of forging is presently below improvement on the AFRC. This features a platform containing a complete database in its coronary heart, with reference to totally different FE software program packages, forging tools, sensors, robotic arms, and supplies fashions. Nevertheless, there are nonetheless gaps in understanding materials behaviours throughout forging, notably throughout ingot-to-billet conversion, which must be properly understood earlier than being applied into the DT platform. The primary goal is to create a totally operational DT of forging titanium alloys with determination making skills and minimised human interactions. At present, the infrastructure nonetheless requires the event and integration of strong supplies fashions to sufficiently seize the bodily microstructure evolution mechanisms.
Thus, the PhD mission may have the next duties:
a. Choose enough variety of samples, with applicable measurement, from an aerospace grade Ti64 billet in as-cast situation.
b. Establish and decide the crucial course of parameters for an onset of recrystallisation:
i. When the as-cast materials is totally recrystallised.
ii. Decide the pressure/pressure fee for the beginning and completion of recrystallisation.
c. Outline DoE for (upstream) processing route together with heat-treatments
i. Upsetting vs. cogging trials
ii. Processing situations and scheduling
d. Run open-die and heat-treatment simulations and execute chosen trials to generate desired wrought merchandise and microstructures/mechanical properties
i. Extract key data from simulations
ii. Check and enhance/develop experimental set-up – die temperature, thermal digicam, DIC
iii. Accumulate, document and analyse dwell course of knowledge
iv. Characterise (totally) as-received and cast/heat-treated elements
e. Constructed course of optimisation instruments for forging
i. Begin from single step processes (upsetting) and transfer in direction of multi-step incremental processing routes (cogging)
ii. Use present optimisation instruments based mostly on Information Analytics, Synthetic Intelligence, Neural Networks and many others. to optimise design
iii. Combine modelling knowledge, dwell course of knowledge, experimental knowledge and processing window data to optimise present step and advise on find out how to carry out subsequent step
iv. Introduce uncertainty and methodology to account for it
v. Resolution making instrument for additional processing or discard present half and begin a brand new
f. Develop purpose-built algorithms for the optimisation of producing based mostly on the necessities of Design for Manufacturing and the holistic view round manufacturing
g. Constructed a GUI/software program to be the platform to manage and run the optimisation of the Digital Twin for forging.
To assist us monitor our recruitment effort, please point out in your electronic mail – cowl/motivation letter the place (globalvacancies.org) you noticed this job posting.